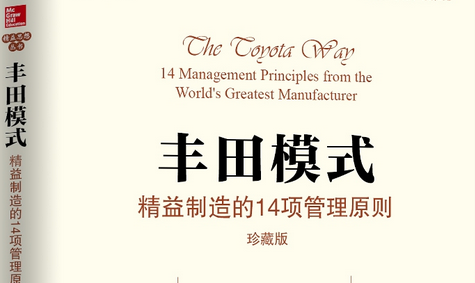
《丰田模式》——把丰田式应用于你的组织
书中摘抄1
精益生产方法的狂热者:已经实行精益生产方法而获致任何程度成功的制造业公司有具经验的人领导转型,这些人几乎全都变成精益生产方法的狂热者。他们通过实际经验,了解精益生产方法的效能,而且很自然地注意到公司里的行政管理与服务作业流程中存在的许许多多浪费情形,就好像小孩看到商店里陈列的糖果一样,也希望把精益方法应用其中。
工作实践 1
发现浪费项,从工作流程开始,以核心任务为第一优先级,审视我所在的团队,寻找可能存在的浪费项。可能是多余的流程、低效的工作方式,或不必要的资源浪费。
现状:团队设计一次评审通过率比较低
举措:在设计文档库增加一个设计评审人员对当前的设计的反馈评语,方便整个团队的设计人员学习其他人的设计经验。
现状:低效反馈。【低效的反馈其实就是一个浪费项,失去了设计评审这个环节的价值,无法给到设计人员建设性的意见】
举措:设计评审SOP
实践心得 1
精益思想需要我们不断进行学习,并在日常工作中不断刻意练习,最终我们才能自然而然的发现工作中的浪费项,让我们洞察浪费更加敏锐。
书中摘抄2
紧密联结的流程会使问题浮现出来。当你把作业程序联结成连续流时,问题就无法再隐藏于存货或排队等候处理之中。当一部门以实时方式从另一个辅助部门收到所需要的信息,将会出现以下两种情形:
若辅助部门速度落后,将使接收信息的部门停工,立刻引起注意。
若辅助部门提供的信息有问题,接收信息的部门会立刻向其提出反馈意见。
因此,问题会立即浮现出来,并进而促成解决问题流程与组织式学习
在技术或服务性质的组织中应用丰田生产方式,其技术性基础骨干是创造连续流。在技术或服务性质的组织中,可使用以下五个步骤来创造连续流:
(1)辨识流程所针对的顾客,以及这些流程想创造与递送的价值。
(2)把重复性流程和独特的非重复性流程区分开来,学习如何把丰田生产方式应用于重复性流程中。(3)绘制流程,以了解流程中有哪些部分是创造价值的活动,以及哪些活动没有创造价值。
(4)创造性地思考如何使用未来状况的价值流程图,以把丰田模式原则广泛应用于这些流程中。
(5)开始实行,并应用PDCA循环以从中学习,再扩展到重复性不强的流程中。
工作实践2
制定机制让上下游形成依赖
软件设计 【解决设计质量存在问题】
0、需求评审没有通过不进入研发流程
1、软件设计没有评审通过,不允许进入开发阶段
2、开发人员,按照设计进行开发前检查设计评审状态,以及设计评审评委的建议,设计问题整改项是否都已经整改完成,并由技术经理再次组织会议把问题项验收通过。
3、没有完成自测和提测演示不交付给下游测试。
思考感悟2
当工作流程被紧密相连,问题就不再隐藏在流程中,任何问题都会立即浮现出来。
因为每个环节都依赖并影响下一个环节。这鼓励了及时的反馈和解决问题的机制。
书中摘抄3
可视化管理制度的目的是改善价值流所谓可视化管理,是指用于工作场所,让人们一眼即可看出应该做什么,以及是否有异于标准之情况发生的任何沟通机制。可视化管理帮助想做好工作的员工能立即看出自己的工作做得如何,可视化管理也可能显示材料或工具等项目该放置于何处、某个项目在此处之数量有多少、执行某件工作的标准程序如何、进行中的工作情况如何,以及其他种种工作流程的重要信息。就最广义的定义而言,可视化管理指的是所有种类的实时信息显示设计,以确保作业与流程的快速且适当执行。在我们的日常生活中就有许多可视化管理的例子,例如交通标志,由于攸关生死,交通标志多半是设计得非常完善的可视化工具,你不需要花时间研究那些交通标志,一眼就可以确知其代表的意义。
工作实践3
对于员工来说人效得分36分算及格,对于技术经理来说团队整体岗位标准达标率超过80%算达标。
拆解人效分析模型细项,及时告诉员工每一项工作自己得了多少分,给员工标杆分数指标、平均分数指标。
工作实践3
大屏晾晒,提供信号 看板或大屏显示器
【坚持今日事今日毕】通过汇总的消息驱动各研发团队负责人跟进团队当日工作完成度
各研发团队负责人在下班前,将收到飞书发送的一个汇总报告消息。
平台将各部门的指标发送到部门负责人;
研发人员在下班前将被告知:当天流水线被构建了多少次,还有哪些流水线未通过。
学习丰田安灯系统,公司每个设备或工作站都装配有安灯系统,如果生产过程中发现问题,操作员(或设备)会将灯打开引起注意,使得问题得到及时处理,避免生产中断或减少问题重复发生。
安灯系统并不是我们理解中的叫停产线,而是在出现问题的地方“亮灯”,呼叫支持团队及时来解决问题。
轮播各团队的流水线、代码质量、case情况,促进各团队竞赛心理。(找到合适的告警阈值,频繁告警可能会打断研发思路)
实践心得3
可视化管理的目的: 可视化管理旨在让团队的工作情况一目了然,一下子就发现问题,使员工清晰了解自己工作的状态,以及工作标准是否得到遵循。
现阶段我们每双周会进行工时人效分析,可能每两周才会去进行分析,两周过去我的团队发生了什么事情,可能需要努力去回忆,而异常的分析和优秀经验的萃取,需要管理者尽快进入现场,达到高效还原现场,及时止损的目的。
而对于员工来说,我当前做的每项 工作,要达成什么样的目标,达成的结果如何,也需要员工自己来尽快进行分析。
两种方式相结合,可以达到自下而上 和 自上而下的 双重改善的效果。
书中摘抄4
务实的解决问题:七个步骤流程
在丰田公司,“五个为什么”的分析方法通常是一个七步骤流程的一部分,这个七步骤流程称为“务实地解决问题”(见图)。在开始使用“五个为什么”分析方法之前,“务实地解决问题”要求你必须先厘清问题—丰田公司本身使用的专有名词称之为“了解情况”,丰田公司教导此方法的训练师发现,最难学习的部分是在进行“五个为什么”分析之前彻底了解情况。
了解情况始于以开放客观的心态观察情况,并把实际情况拿来和标准相对照比较,为厘清问题,起始点是必须亲自到问题的发生地点(现地现物),这可能包括使用帕累托分析(Pareto Analysis)来排定多个问题的优先级。
帕累托图是根据各问题的严重性、发生频率、性质或源头,使用柱状图来整理排列它们,呈现它们的程度,以显示什么问题最重要,这大概是丰田公司最常使用的统计分析工具,虽简单却非常有用。
此时,你也想制定改善目标,首先试图找出原因点(point of cause, POC),在哪里观察到问题,可能原因为何。这将引导你向上溯源至根本原因的邻近区,你可以使用“五个为什么”分析找出根本原因。此流程的最终目的是产生并执行对策,评估对策的执行结果,若对策有效,方能变成新标准化方法的一部分。
在丰田公司,第7个步骤—把新流程标准化非常重要,标准化及共同学习是持续改善的基础,若不把改善的新流程标准化,学习就会掉入一个黑洞,被遗失、遗忘,无法再继续改善。丰田公司最强调的并不是工具、技巧、方法,而是思考问题的方式与解决问题的方法,在丰田公司,解决问题时,思考占了80%,工具只占20%